Polymer files #5
Design in Motion: The Bearing
Learn about the mechanics and history of the ball bearing, from its invention in the early century to its modern-day applications in the cycling industry.
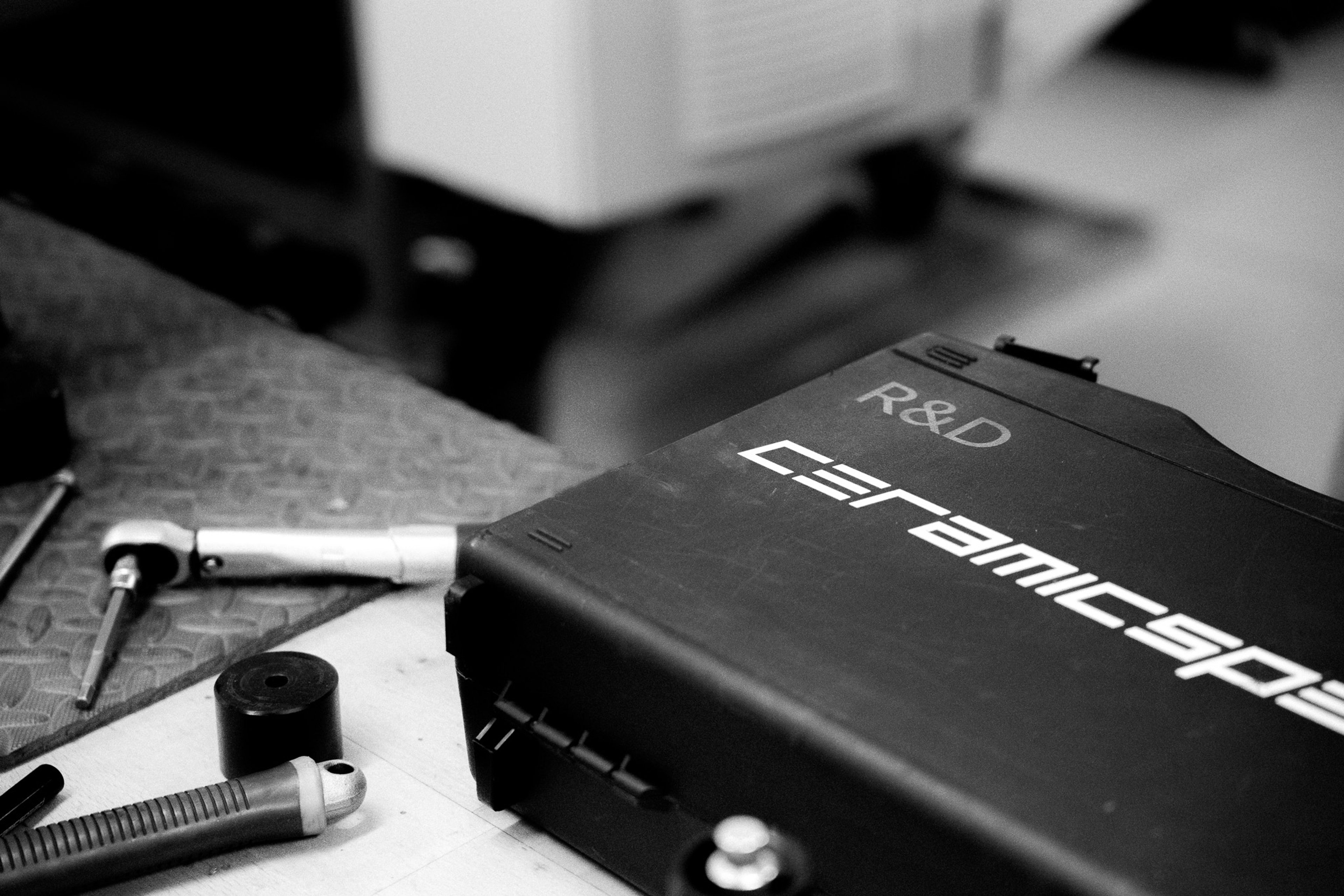
A ball bearing is a precision-engineered component that is widely used in machinery to facilitate smooth motion by minimizing friction. It consists of small, spherical balls that roll between two ring-shaped tracks, reducing surface contact and enhancing efficiency.
This design enables the bearing to support both radial and axial loads, making it suitable for versatile applications in various mechanical systems. Ball bearings are essential in numerous devices, ranging from automotive parts to industrial machinery, as they embody a fundamental concept in engineering for promoting fluid and reliable movement.
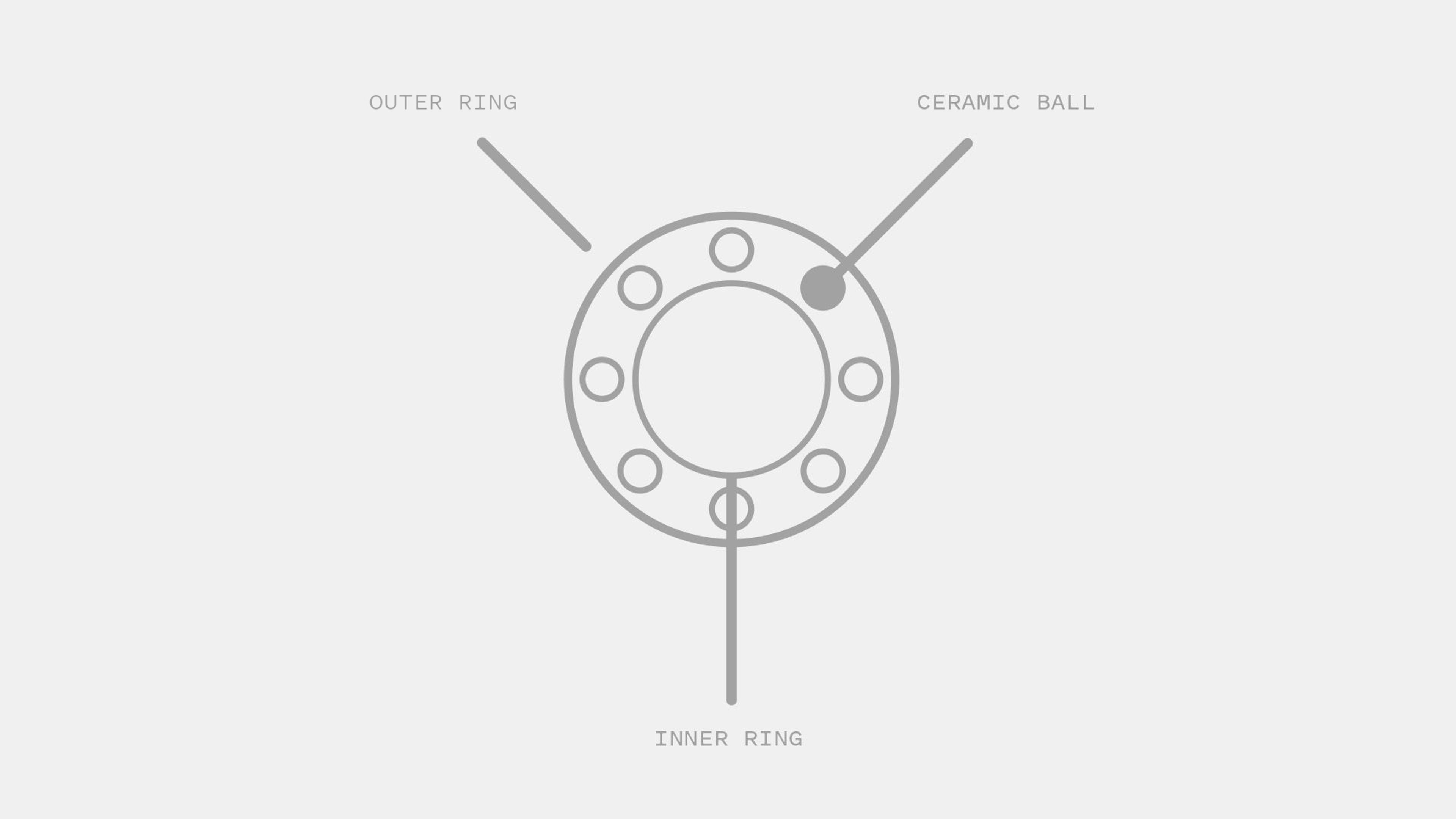
The invention of the ball bearing can be traced back to ancient times, with evidence suggesting its use in Roman and Egyptian civilizations. However, the more recognizable and documented development occurred during the Renaissance, with Leonardo da Vinci's sketches and conceptualization of ball bearings (1498-1500).
Da Vinci's insights laid the foundation for the modern ball bearing, and further improvements and innovations during the Industrial Revolution solidified its significance in machinery and mechanical engineering.
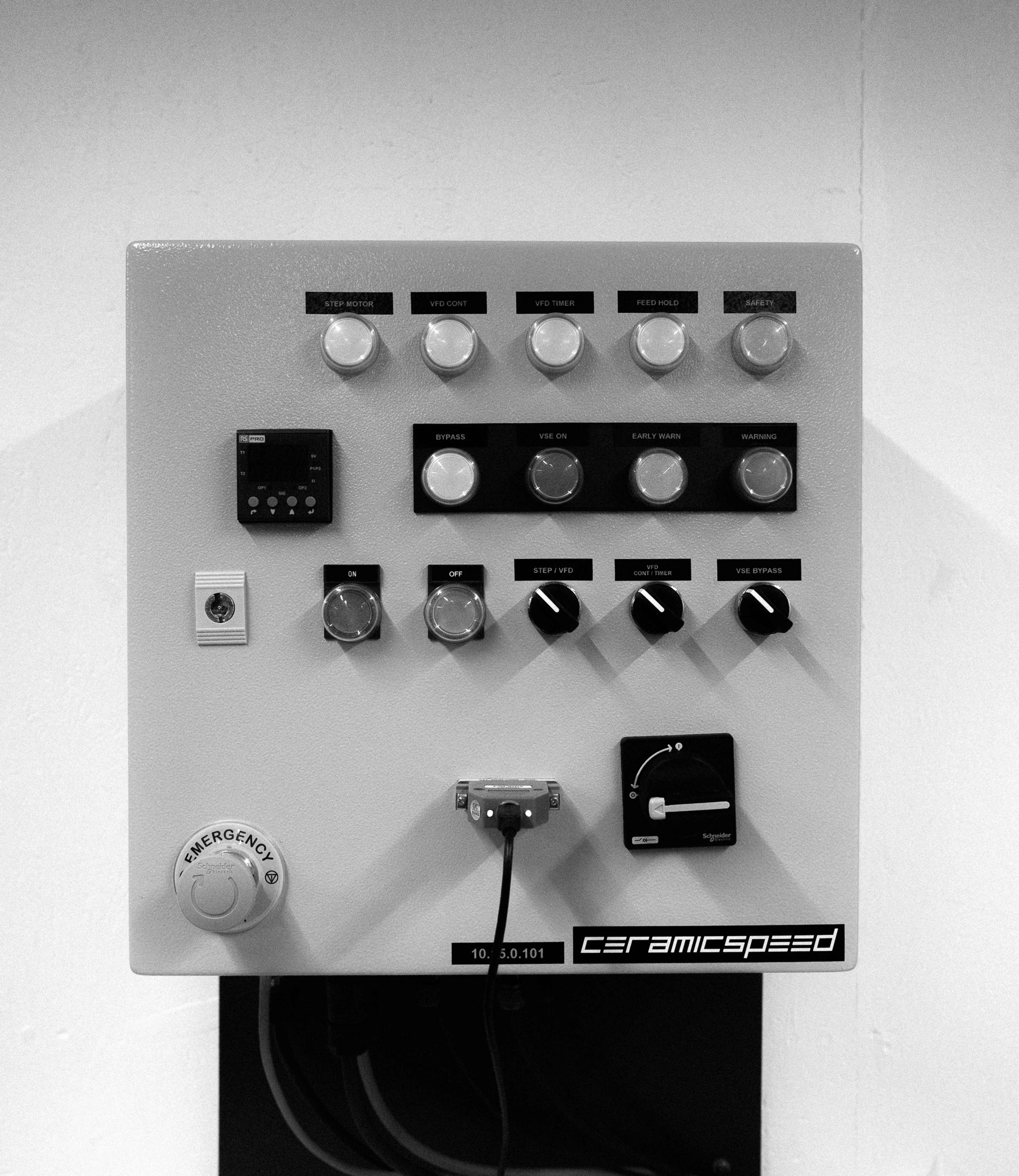
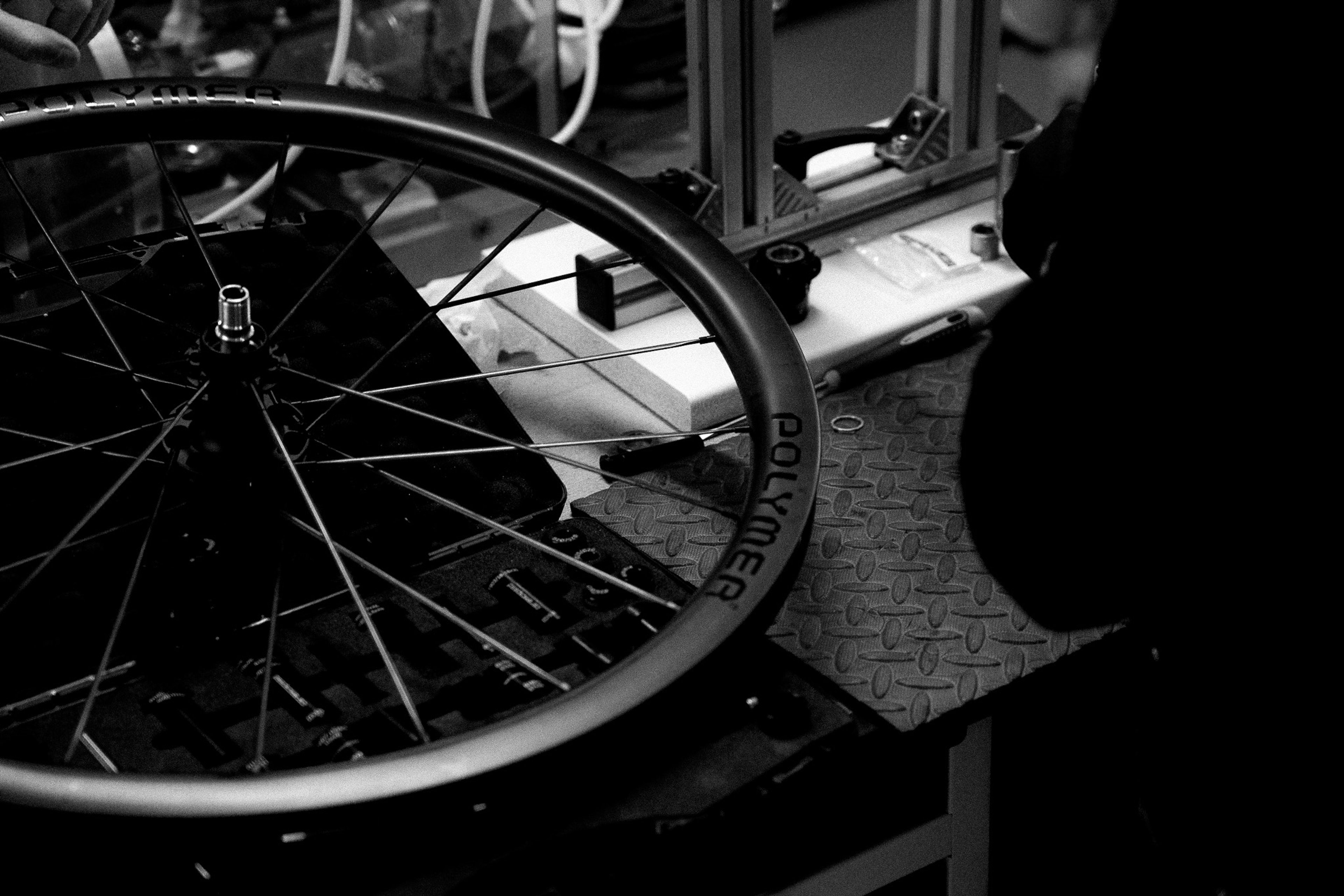
In the cycling industry, ball bearings are widely used in various crucial components. They play a key role in the smooth functioning of wheel hubs, bottom brackets, and headset assemblies in bicycles.
Ball bearings reduce friction and enable efficient rotation, making a significant contribution to the overall performance and durability of cycling equipment. The precise application of ball bearings in these components enhances the rider's experience by ensuring smooth, responsive, and reliable operation with every pedal stroke.
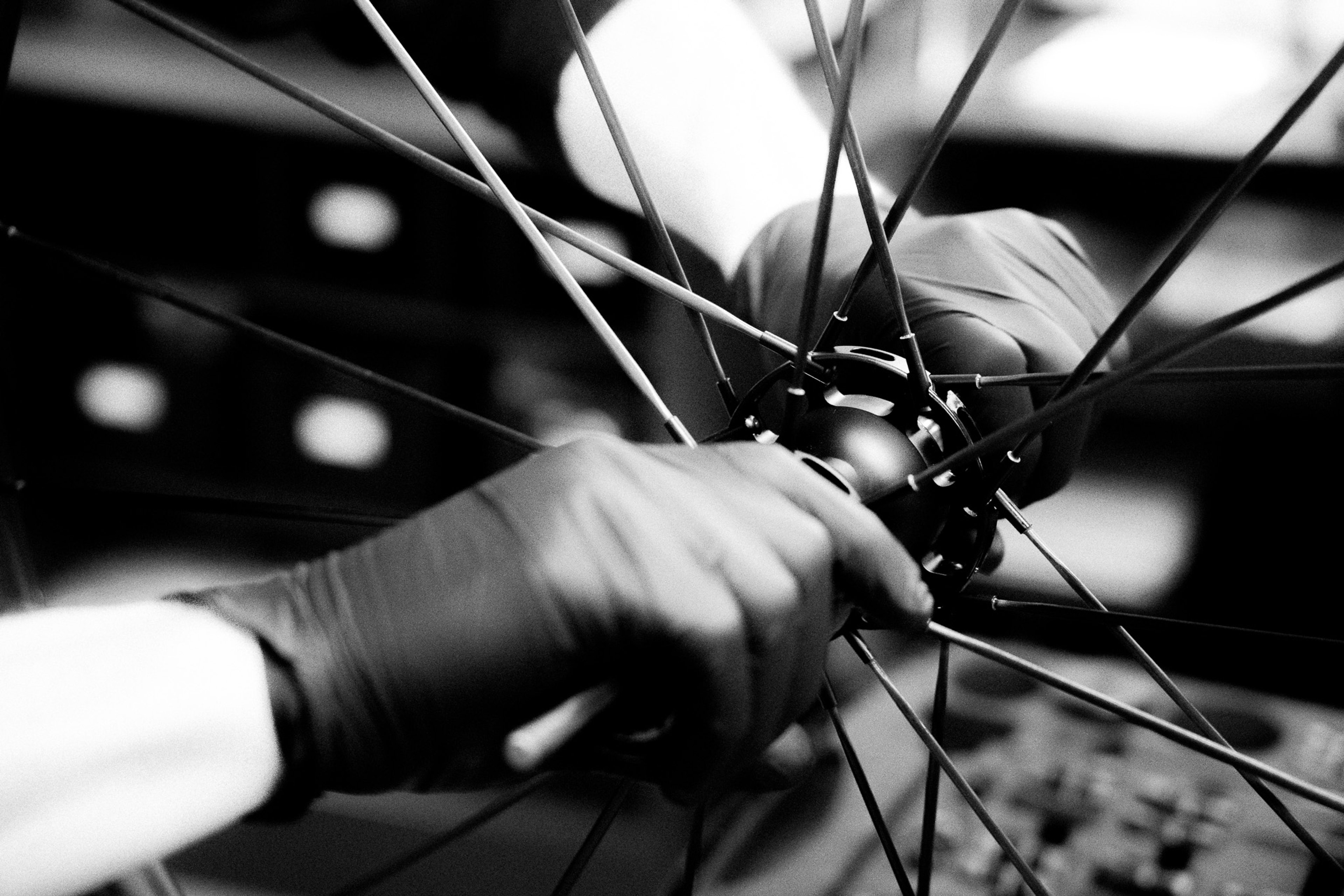
For years, the cycling industry has been associated with the relentless pursuit of small improvements, and as a result, ceramic bearings have gained popularity in this industry due to their many advantages. One of the main benefits is their ability to greatly reduce friction. It enables smoother and more efficient rotation, leading to enhanced performance and durability of cycling equipment.
When CeramicSpeed entered the bike industry in 2004, very little was known about the longevity of ceramic bearings. The consensus was that their primary benefit was the reduction in friction. However, CeramicSpeed's commitment to precision engineering and innovation has made them a standout player in enhancing cycling performance through the fine-tuning of ball bearing technology.
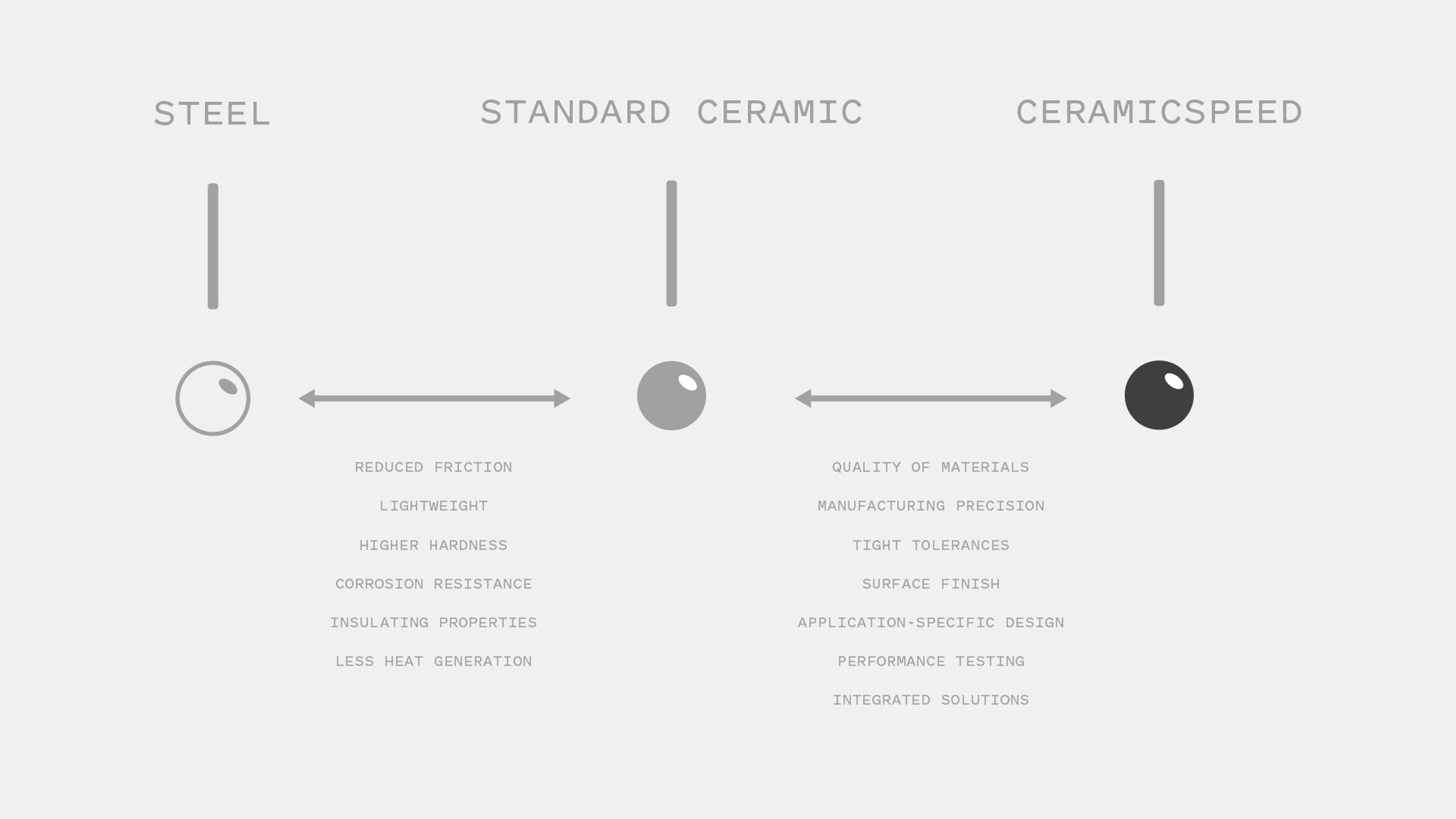
To fully grasp the distinction between a traditional steel ball and a CeramicSpeed ball, it is necessary to delve into the comparison between a bearing composed of steel and one composed of ceramic.
Ceramic bearings offer several advantages over their steel counterparts. Firstly, ceramic materials have a much lower coefficient of friction, which means that they generate less heat and operate more efficiently. This allows for smoother and more efficient rotation, leading to improved overall performance and durability.
Additionally, ceramic bearings are also known for their superior hardness and resistance to wear. This means that they have a longer lifespan and require less maintenance compared to steel bearings. Several factors, including weather, lubricant choice, and service expertise, determine the frequency of bearing maintenance for its long lifespan.
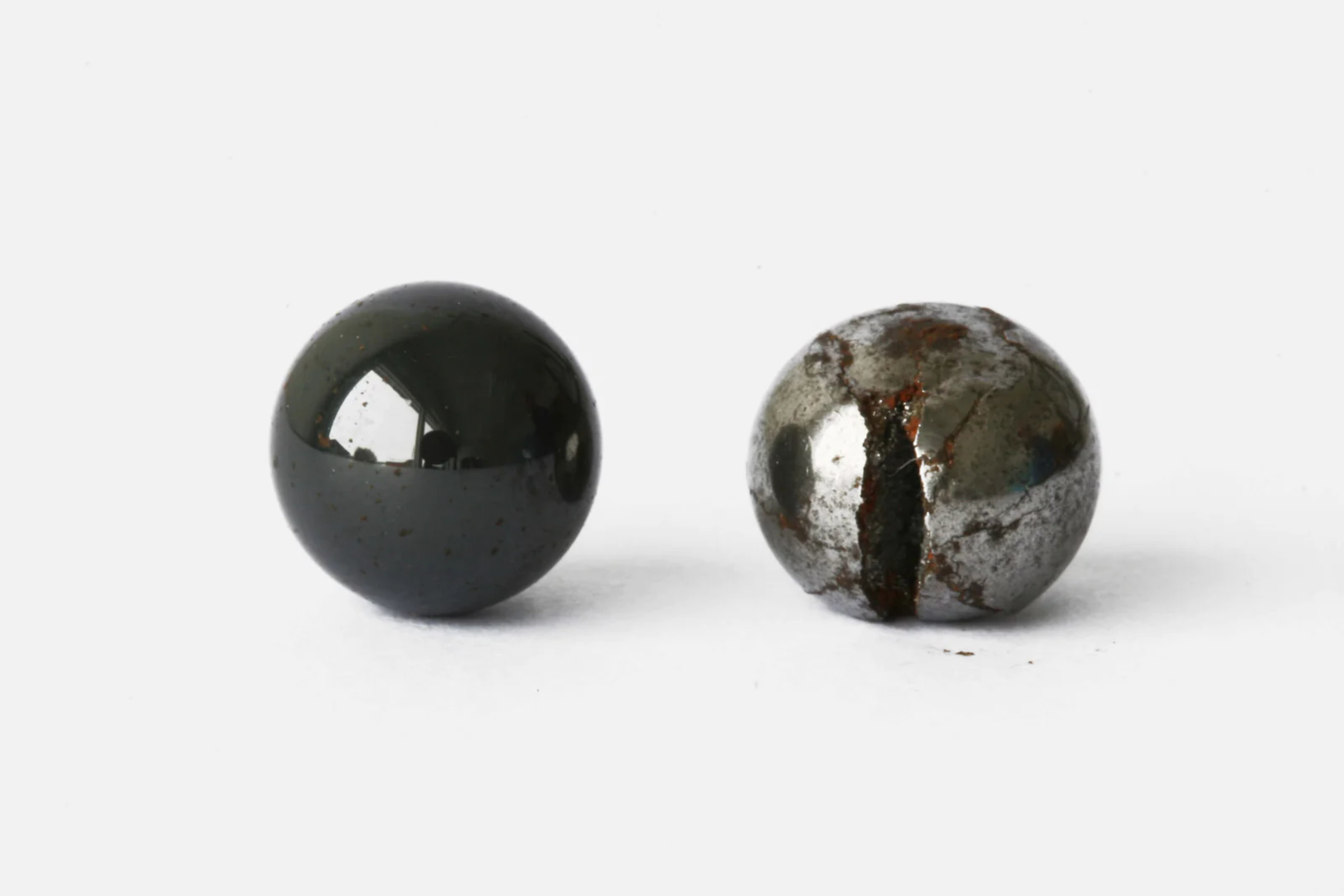
CeramicSpeed's dedication to precision engineering and innovation has led to the creation of a superior product that surpasses competitors in various aspects. Their ceramic balls undergo a thorough quality check, fine-tuning, and specific assembly to guarantee the best performance compared to standard ceramic balls.
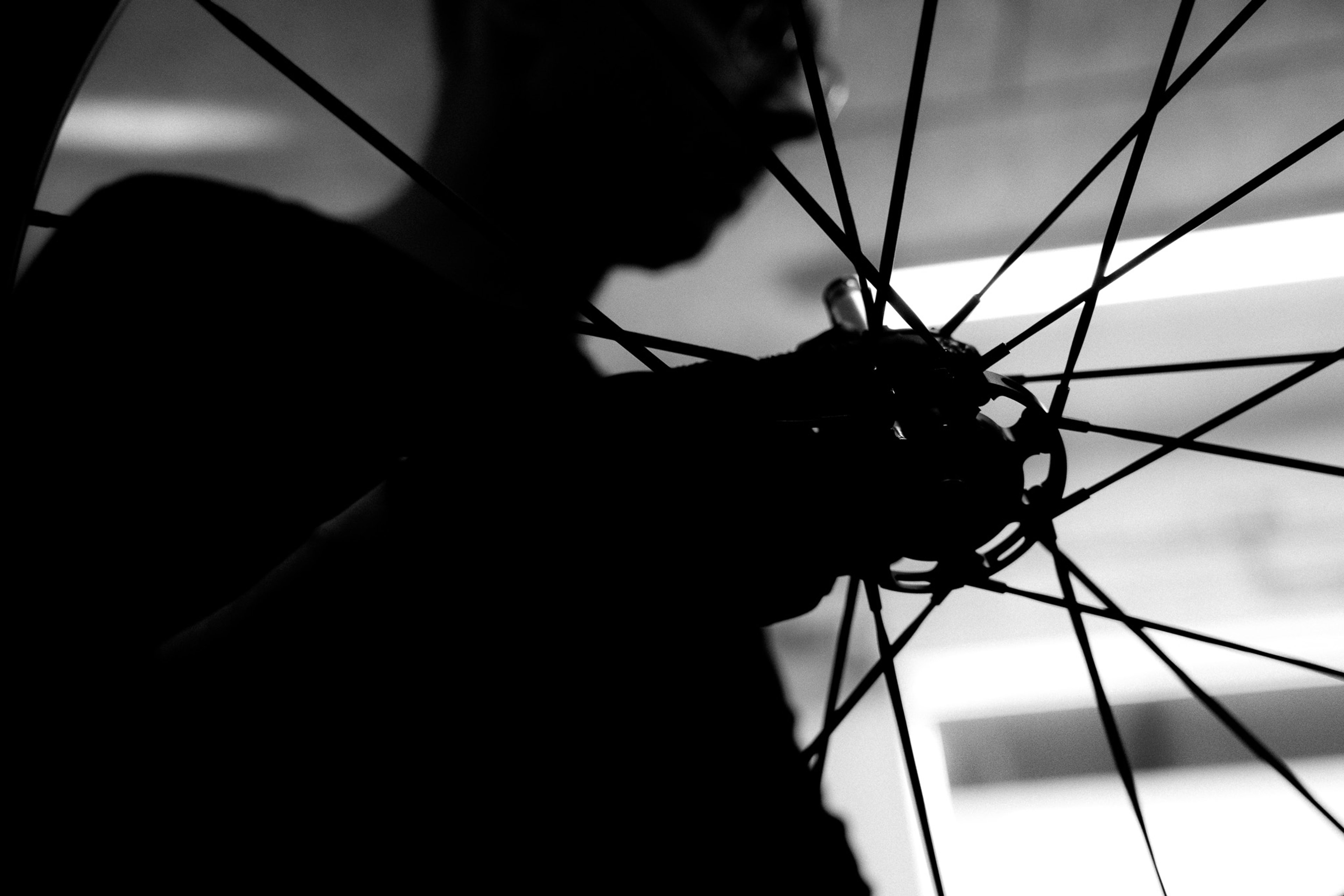
To push the boundaries even further, CeramicSpeed recognizes that each bearing application is unique. This implies that the performance of the bearings and the wheel as a whole is greatly influenced by factors such as different wheels, hubs, and spoke tension. The R&D team aims to minimize friction in the wheels without causing any lateral movement.
They achieve this delicate balance by testing the optimal radial clearance, which ensures the best spinning, just below the point where the wheels start to exhibit lateral movement. In essence, they push the limits while maintaining safety, similar to leaning into a sharp corner without losing control.
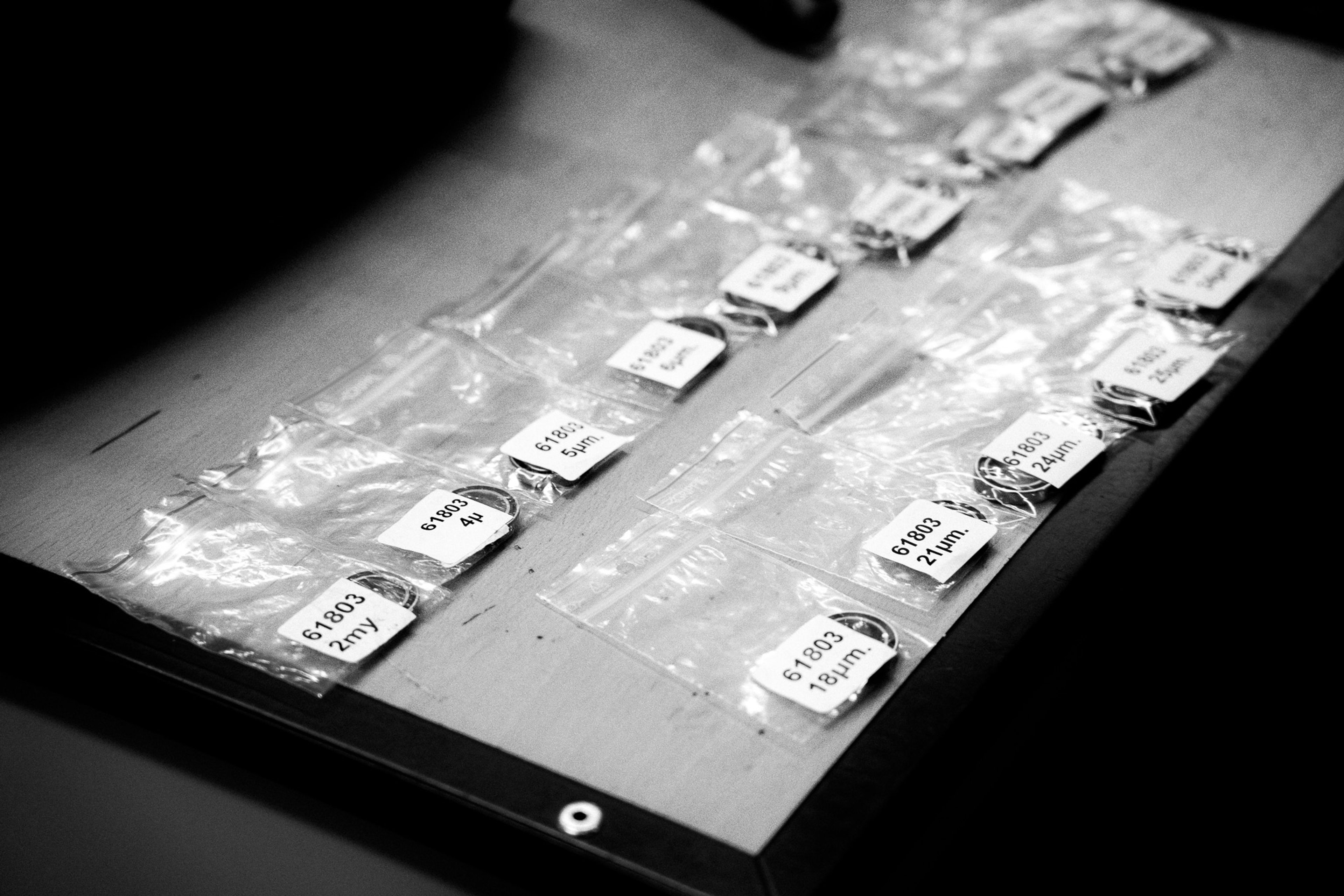
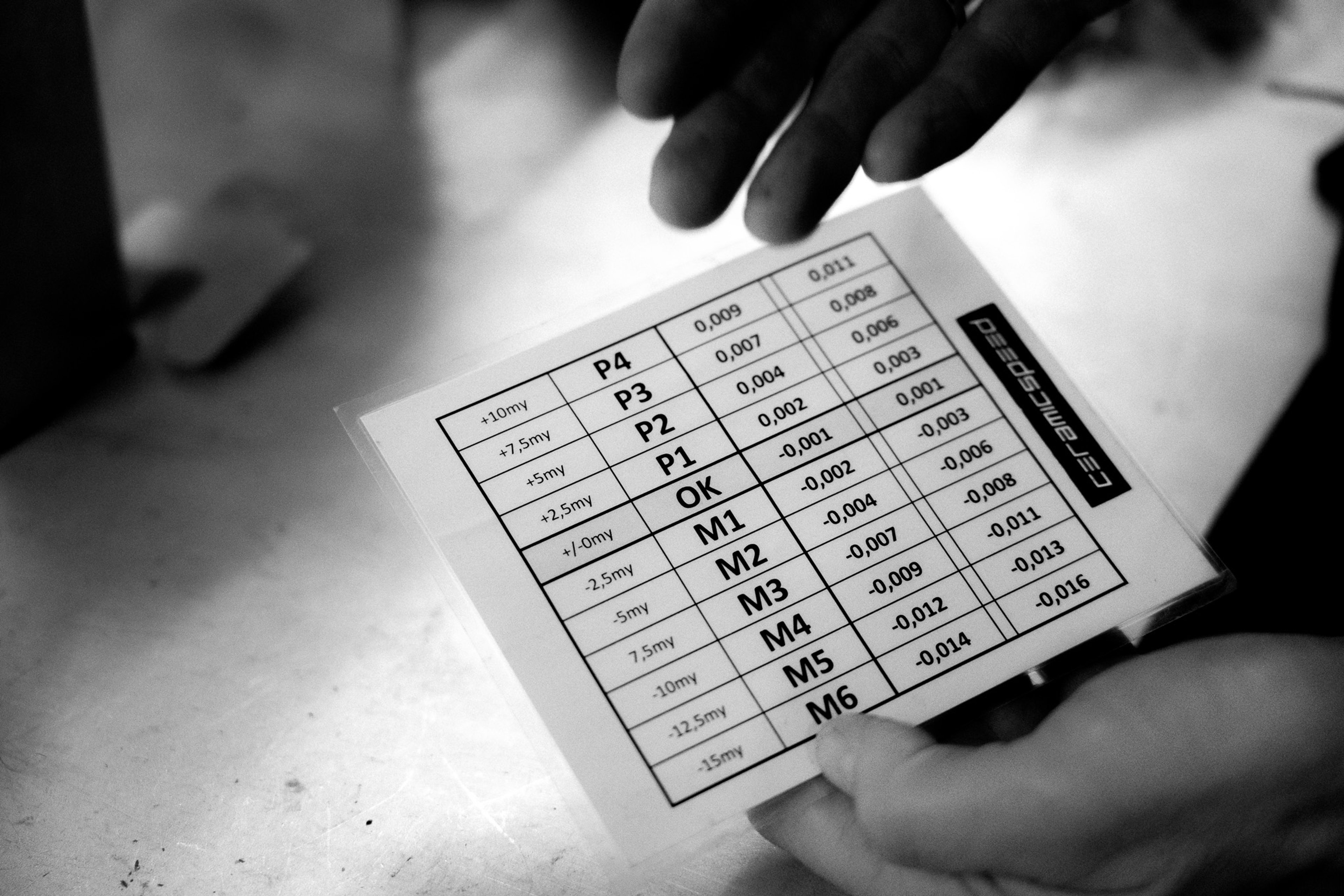
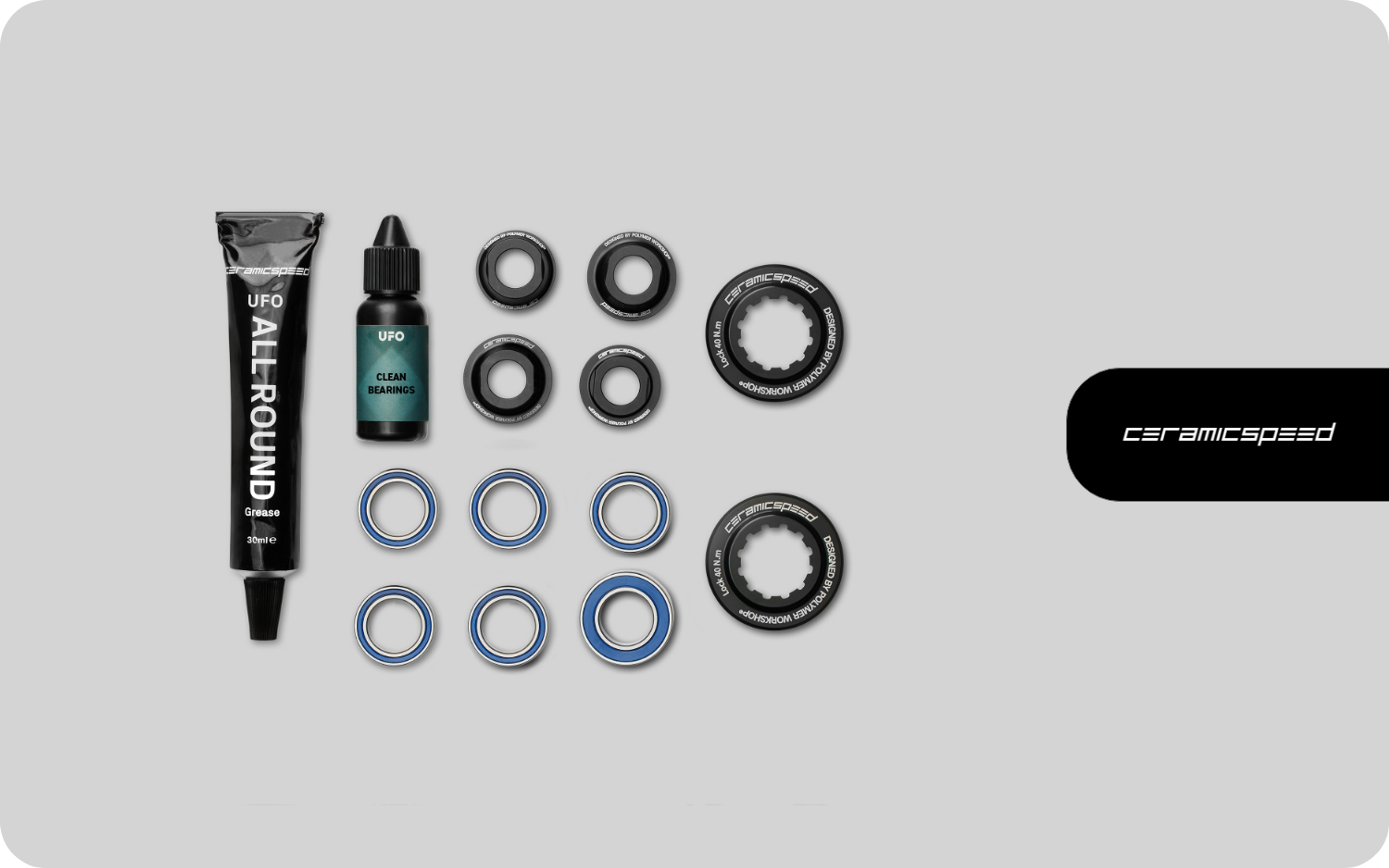
CeramicSpeed Upgrade Kit
The outcome is a remarkable demonstration of performance and incremental improvements. Through our collaboration, CeramicSpeed has successfully designed and produced a custom-fitted bearing specifically tailored for the Polymer Workshop wheelsets. This partnership has allowed us to work closely with CeramicSpeed to ensure the development of bearings that are perfectly suited to the unique requirements of the Polymer Workshop hub.
Care and Maintenance
To ensure optimal efficiency and extend the lifespan of your CeramicSpeed bearings, regular preventative maintenance is important. The frequency of maintenance may vary depending on the climate and typical riding conditions*. In some cases, more frequent maintenance or the use of a different type of grease may be necessary. The following recommendations are based on using CeramicSpeed All Round blue grease.
For CeramicSpeed Bottom Brackets and Wheel Bearings, it is recommended to perform maintenance every 5,000-8,000 km or 3,000-5,000 miles, or annually. These bearings generally last five times longer compared to standard bearings. As for CeramicSpeed headset bearings, most riders can perform maintenance once per year.