Polymer files #8
Design in Motion | Disc Brake Rotors
Understand the mechanics and history of the disc brake system. This knowledge will help you appreciate their importance and make informed decisions about maintenance and upgrades for your bicycle.
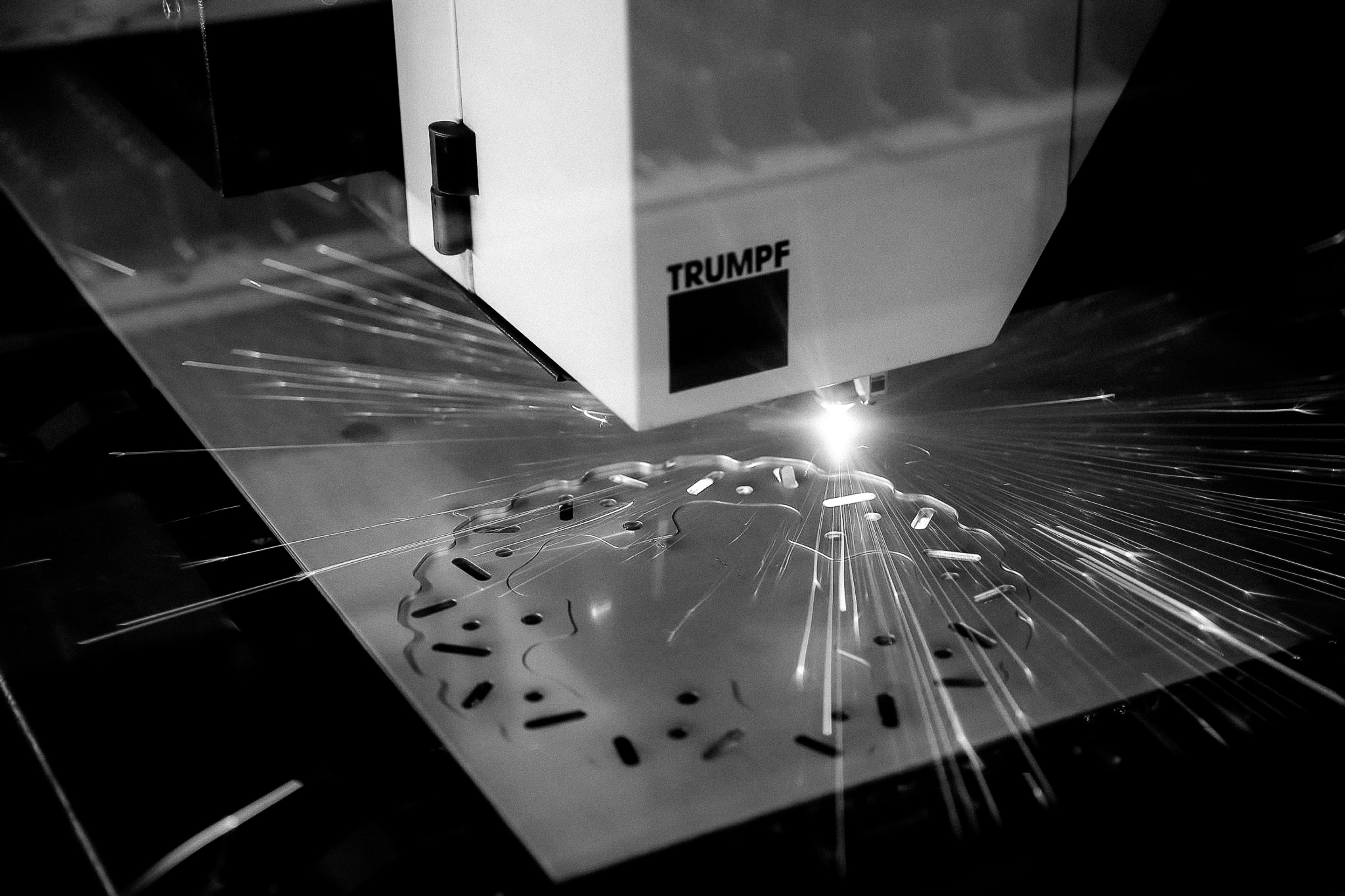
Disc brakes have existed for over a century, initially used in industrial applications like trains before being adapted for cars. The first practical disc brake system for cars was patented by Frederick William Lanchester in 1902. However, it wasn't until the 1950s and 1960s that disc brakes gained widespread use in high-performance vehicles and eventually in mainstream cars.
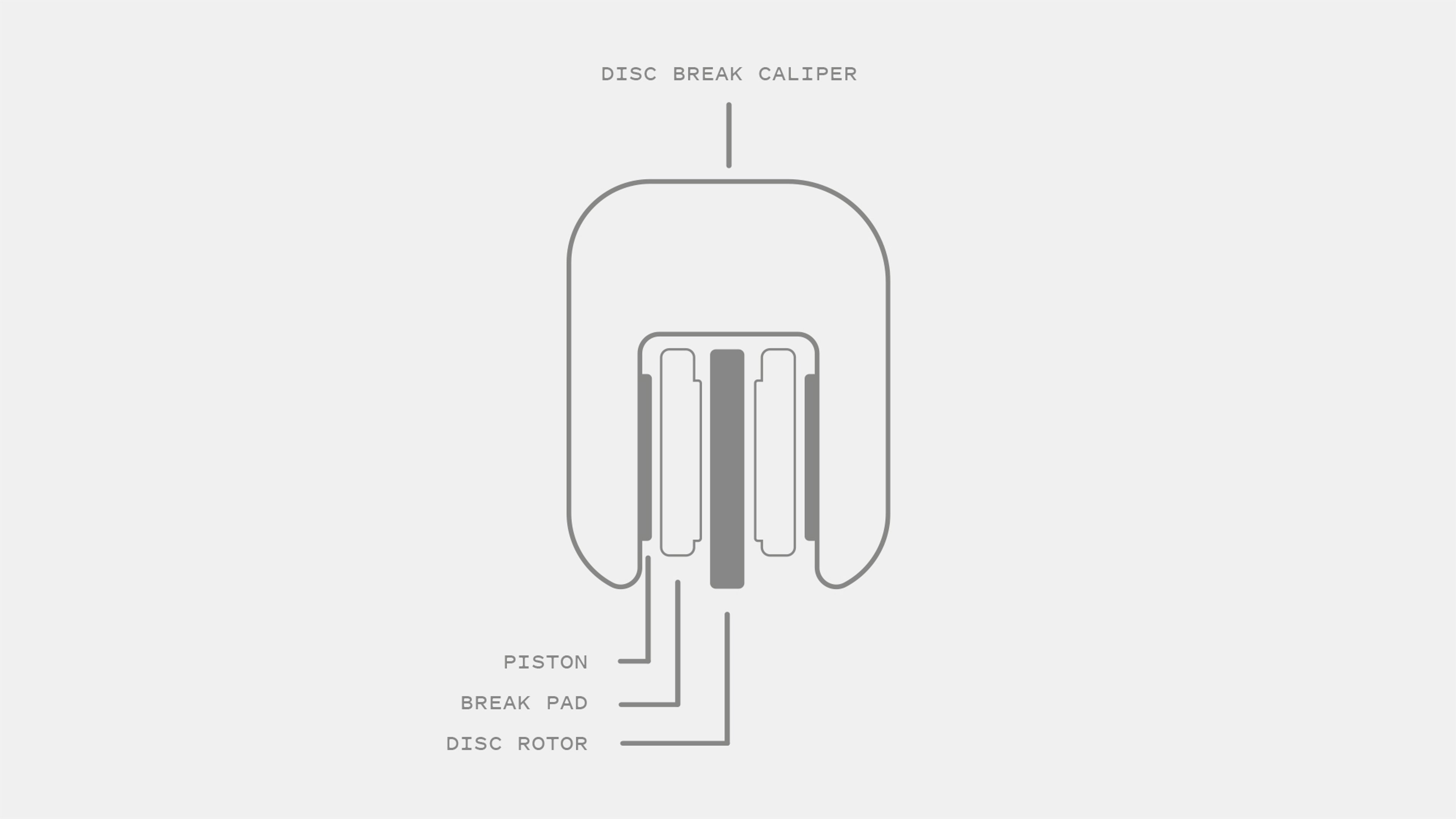
A disc brake is a brake system that uses calipers to squeeze pads against a disc or rotor to create friction. This friction, which can be either abrasive or adherent, slows down the rotation of a shaft, such as an axle. It can reduce the shaft's rotational speed or hold it stationary. This process transforms kinetic energy into heat, which must be dissipated when it exceeds certain material thresholds.
In cycling, the disc brake rotor is a part that connects to a bicycle wheel hub and acts as the braking surface in a disc brake system. Disc brake rotors come in various sizes to accommodate different riding disciplines and terrains. Common sizes for road and gravel cycling include 160mm and 140mm.
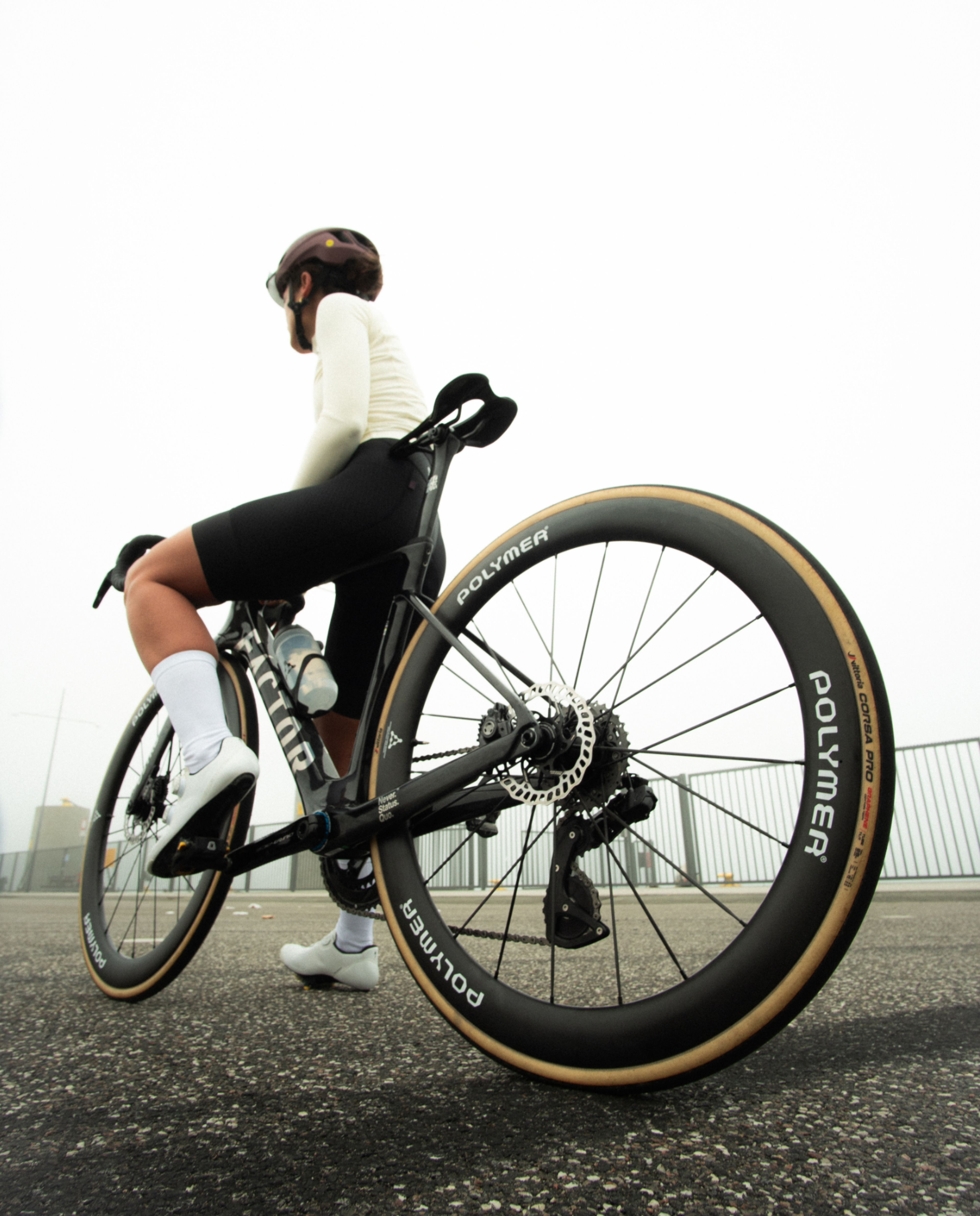
Understanding the rotor's function can assist in selecting the right size. When a piston pushes brake pads against the rotor, friction slows the wheel's rotation. 160mm rotors, being further from the rotating axle, offer more leverage and torque to halt rotation than the 140mm.
However, a 140mm rotor can provide a comparable braking experience for lighter riders. It also offers minor aerodynamic advantages and is about 30g lighter than the 160mm rotor. Therefore, your choice should be based on the terrain, system weight, and necessary braking performance needed.
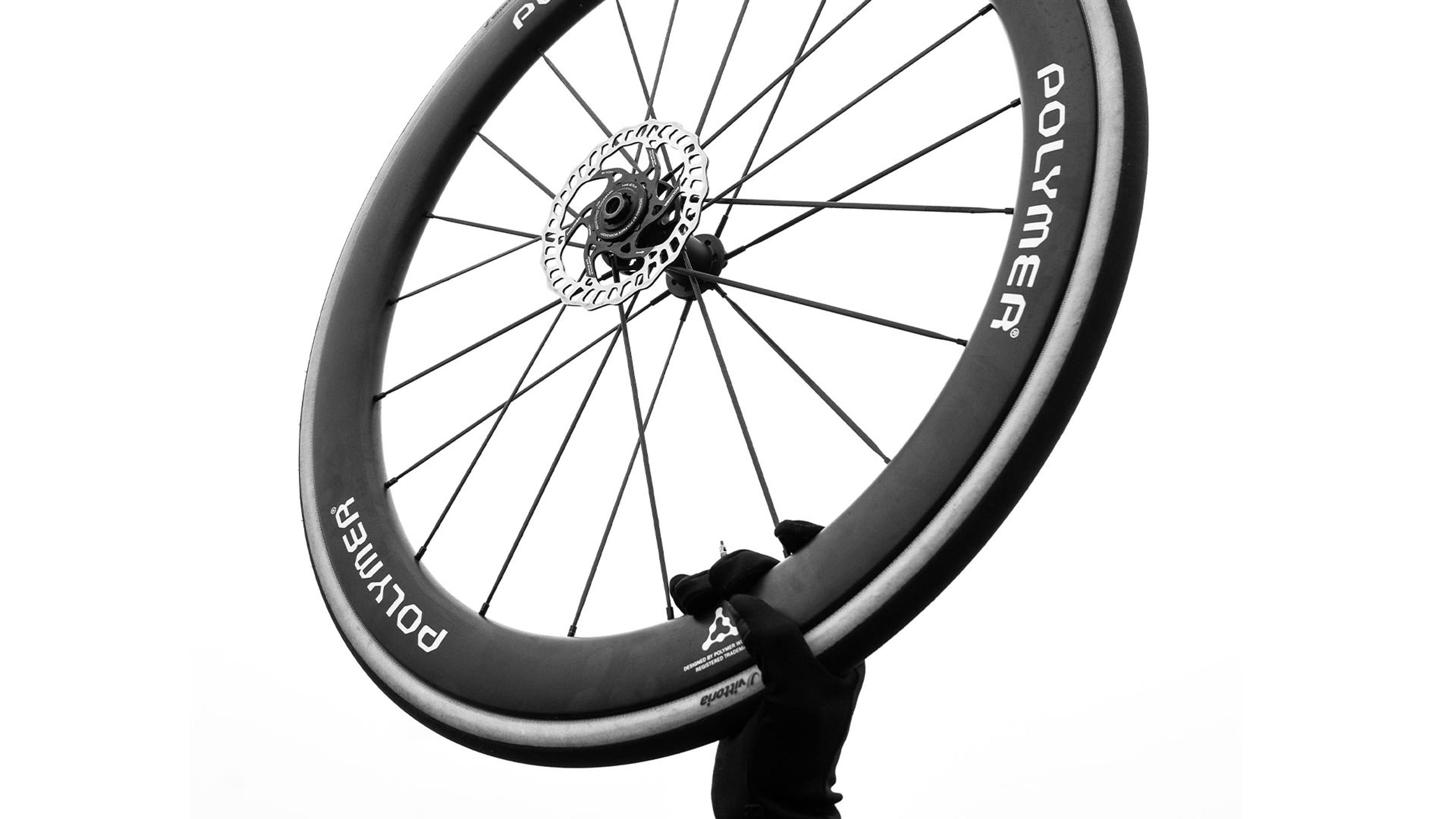
Production and Materials
For Industrias Galfer, the production process starts in the R&D Department, which is responsible for launching new products. The materials are developed in our labs, followed by chemical and physical tests. Once this phase is complete, further tests are conducted on a vehicle to decide if they'll move into production. The Methodology Department works with the Engineering Department to design the production processes. Lastly, the Quality Department certifies our products' quality and reliability based on ISO standards.
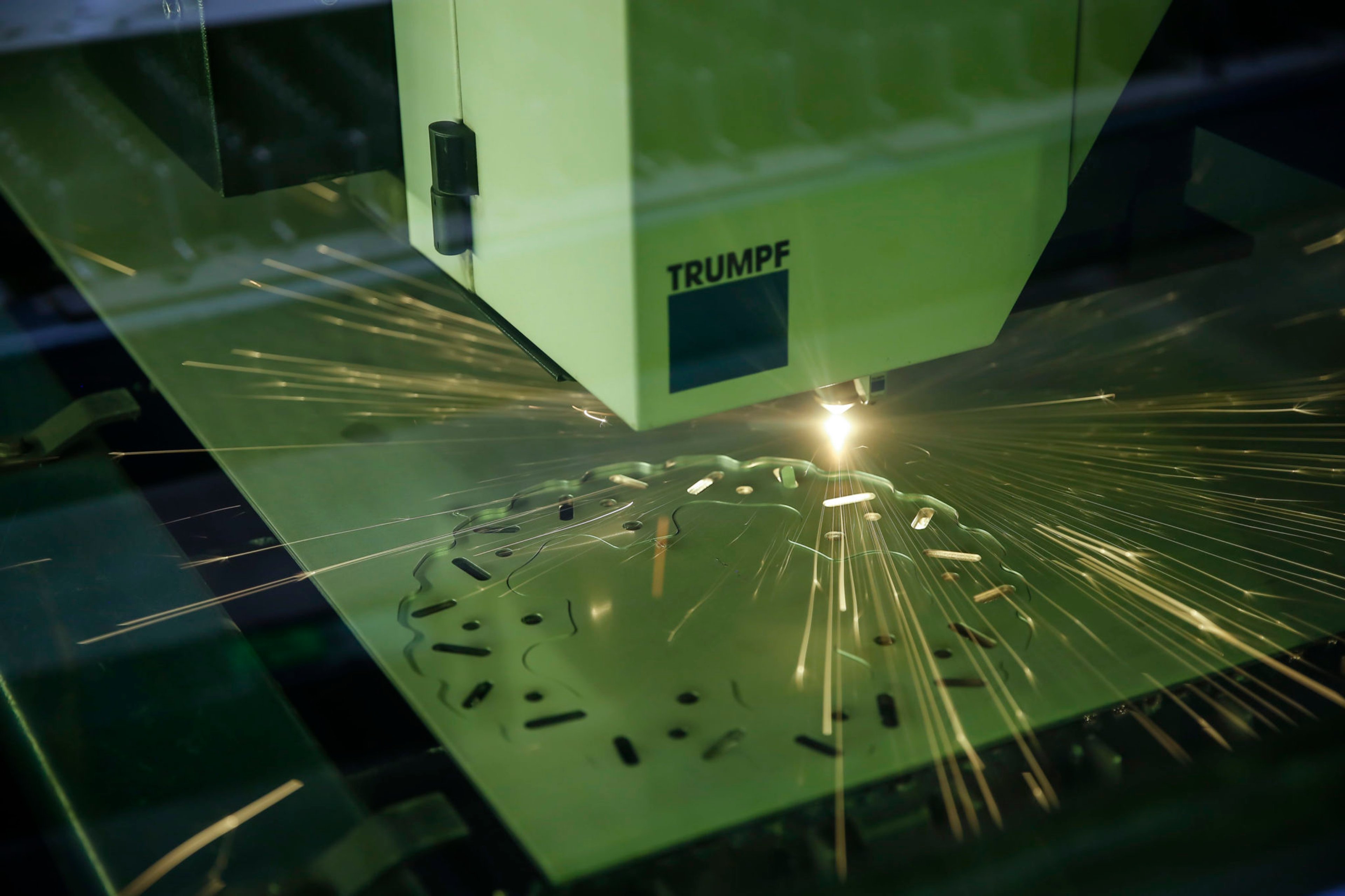
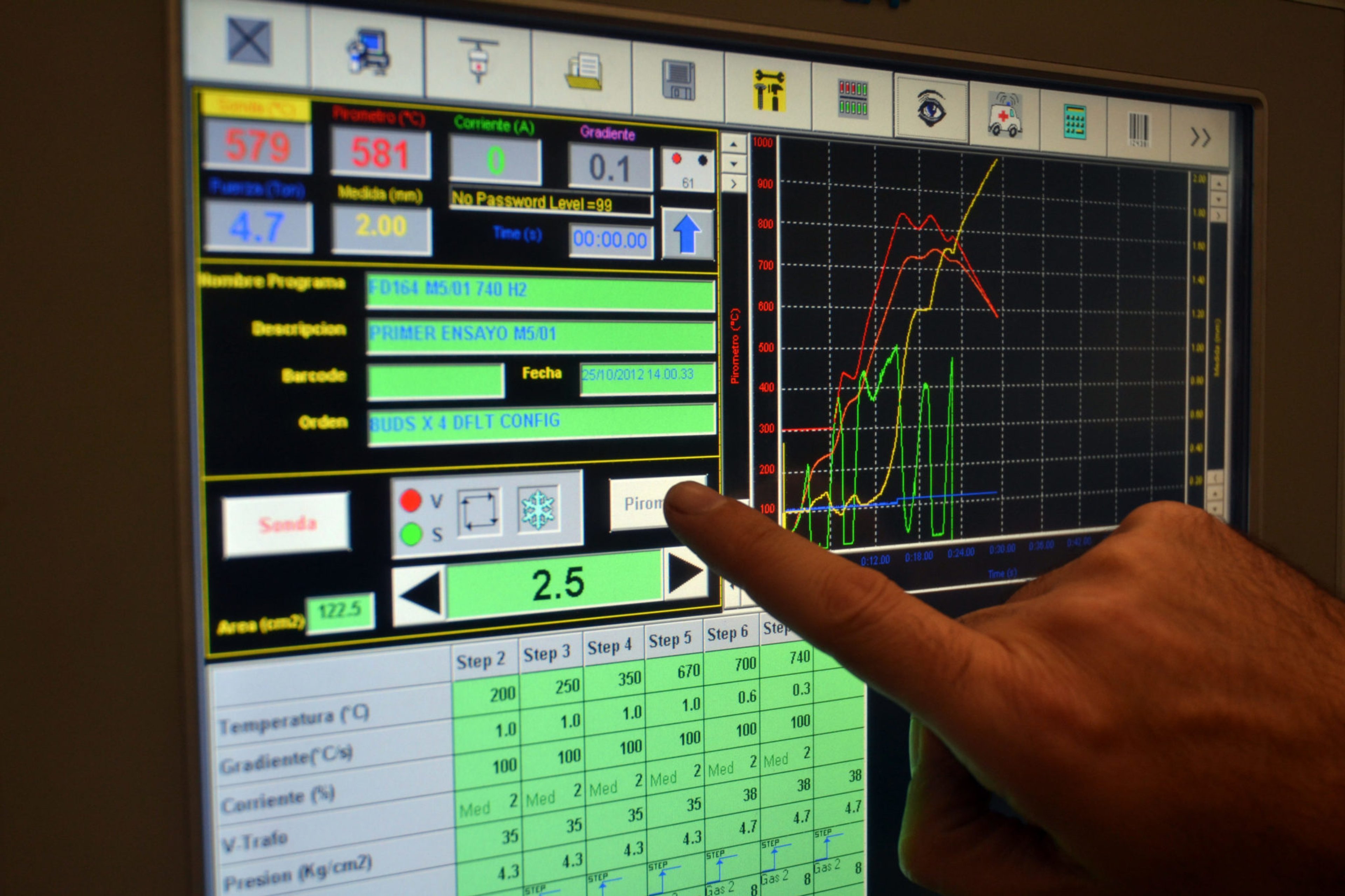
The most basic disc brake rotor is stamped from a stainless steel sheet. Higher-priced rotors use complex structures and undergo multiple coatings and treatments to boost braking performance. When designing rotors, manufacturers prioritize heat conduction, braking performance, weight, and long-term durability.
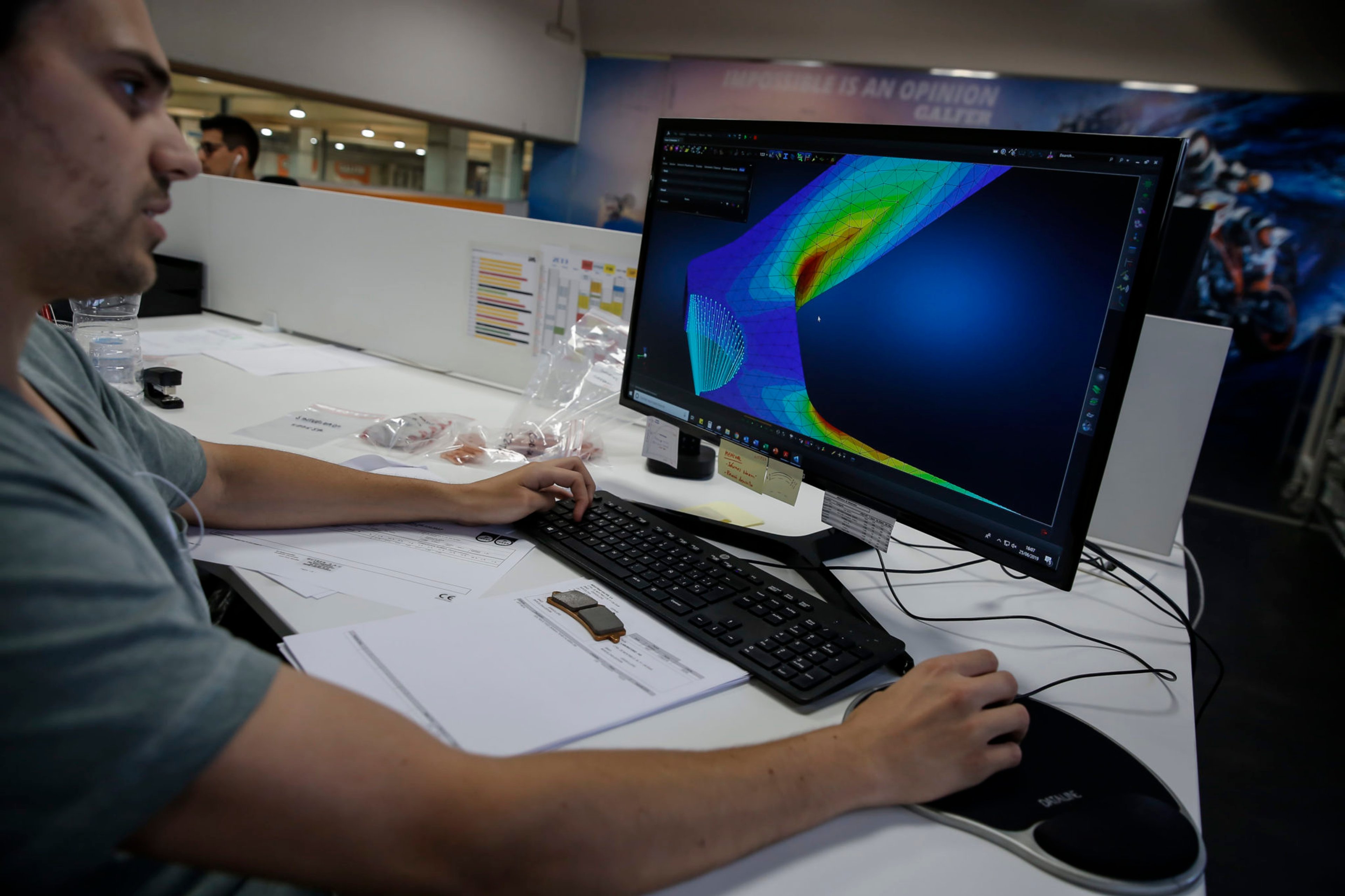
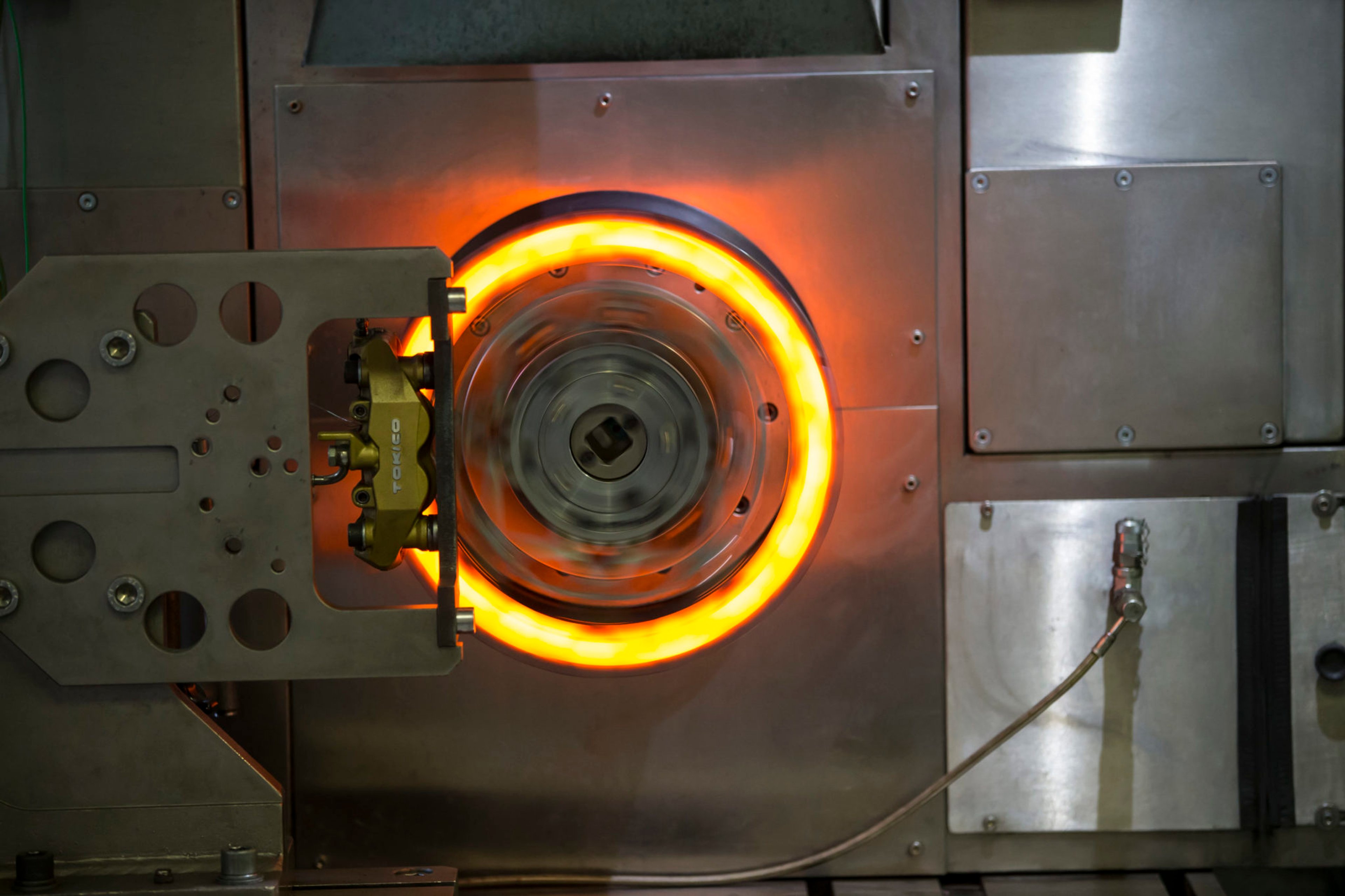
In this highly competitive market, Galfer understand that the only way to stay ahead of the competitors and remain a global leader in manufacturing braking systems is through continuous improvement. The R&D department team combines their passion and enthusiasm with cutting-edge technology to produce the best final product. This product, with enhanced braking power, reduced wear, and decreased noise, is favored by leading brands in the industry.
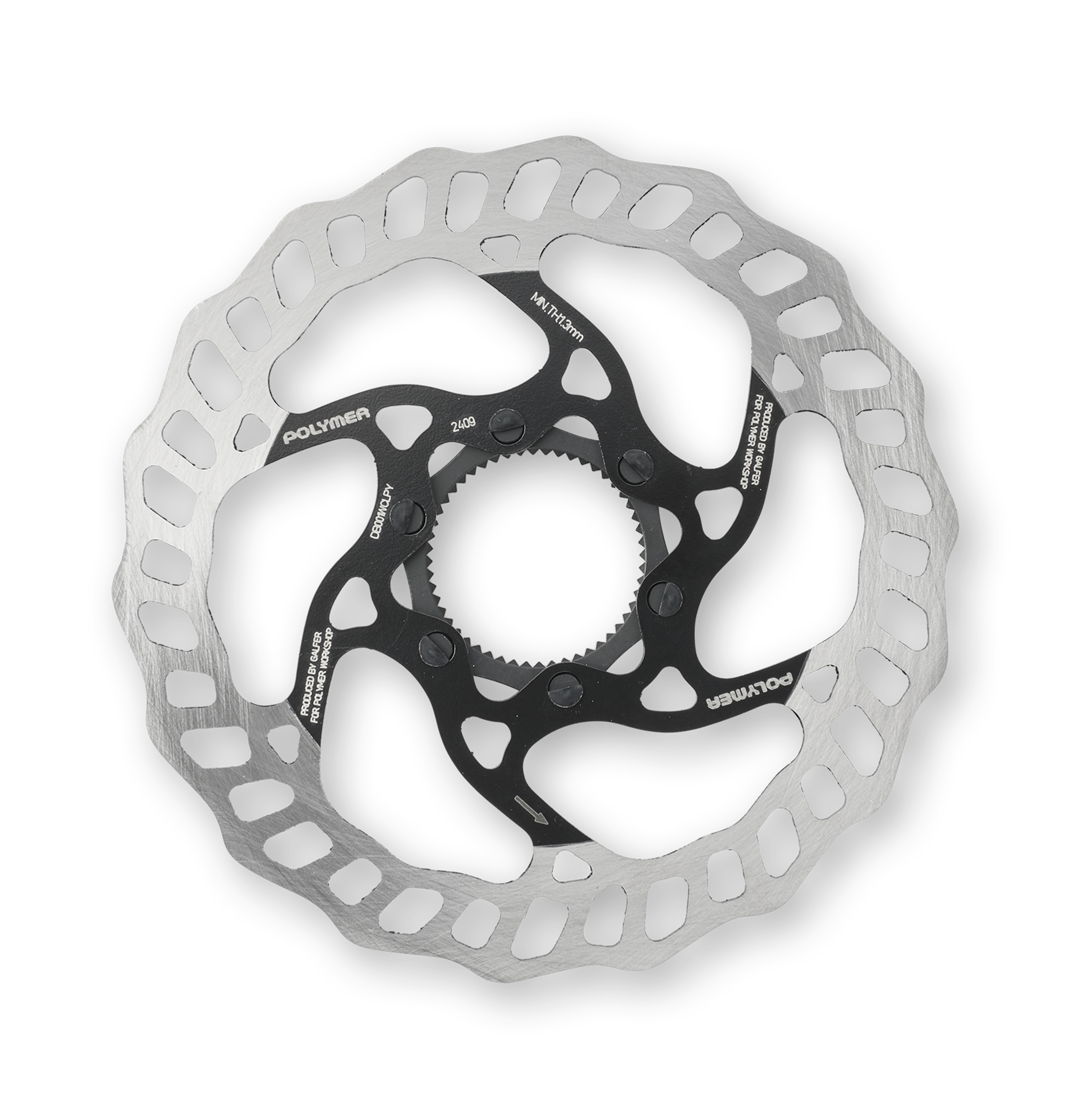
Polymer Workshop® + Galfer
Polymer Workshop® has collaborated with the Spanish company, Galfer, to develop a new exclusive 140mm version of their signature Disc Wave® Rotor.
Laser-cut from high-carbon stainless steel, utilizing Galfer’s top-competition technology. The rotors undergo both anti-corrosion and heat treatments to enhance their hardness properties.